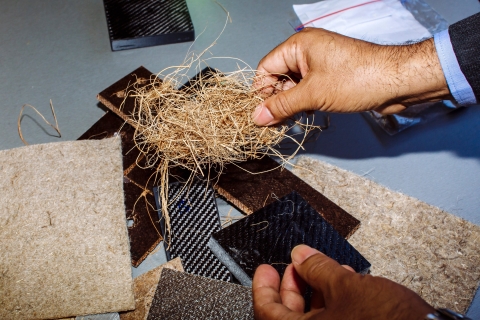
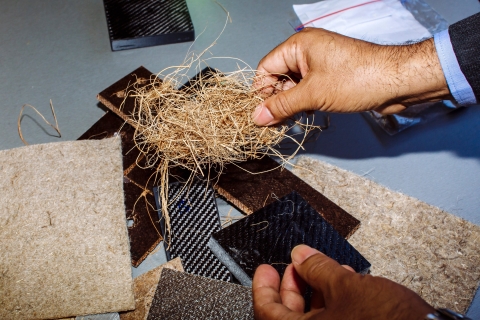
Pioneering greener composites: how flax fibres and cross-border collaboration are reshaping the future of sustainable manufacturing.
7 minutes
The FLOWER research project stands as a beacon of innovation and sustainability, advancing the field of natural-fibre composites and their diverse applications. Here we celebrate its achievements and the future potential of this ground-breaking research.
Enhancing sustainability in the composites industry
Composites are widely used across various industries, making up about 20% of a car's weight and nearly all of a pleasure boat's weight. Currently, these composites consist of glass fibres and non-recyclable resin. The composite industry has a huge market, including aerospace, marine and automotive, so the challenge lies in bringing greater sustainability to these sectors.
The FLOWER project (Flax composites, LOW weight, End of life and Recycling) aimed to reduce the environmental impact of composite materials by developing innovative bio-based composites with natural flax fibres.
The project successfully developed new natural fibre composites that are cost-effective, environmentally friendly, lightweight, and viable alternatives to glass fibre composites for the automotive, marine, and point-of-sales advertising sectors. The products were designed with a full life cycle approach to ensure the new materials are either biodegradable or recyclable at the end of their life.
The University of Portsmouth was one of the four academic partners in the project. Through the Portsmouth Centre for Advanced Materials and Manufacturing (PCAMM), the University has extensive experience in using natural fibres for advanced applications.
Product development and market impact
The composite market lacks suitable alternative products because bio-based materials are often designed for the textile industry, and not well-suited to the needs of composites. This presents a significant barrier to development.
FLOWER strived to address industrial demand by developing two types of semi-finished products:
-
Non-woven reinforcements with a low grammage (50 gsm compared to the current 200 gsm) or with recyclable polymers.
-
Long fibre reinforcements for structural applications.
Additionally, biodegradable and bio-based thermoplastics were explored to ensure end-of-life sustainability.

FLOWER was co-financed by the European Regional Development Fund (ERDF) within the framework of the INTERREG France (Manche) England cross-border cooperation program.
Key outcomes and achievements
The FLOWER research project has set a new standard for innovation and sustainability in the composites industry by demonstrating the immense potential of natural-fibre composites.
Three prototypes have been developed for key applications in the marine, automotive, and advertising sectors. These prototypes are close to market readiness, showcasing the practical applications of flax-fibre composites.
The project's success was recognized with the prestigious JEC Award for Innovation in 2022, a testament to its impact in the composites sector.
Replacing plastic-based materials
The FLOWER project also investigated whether natural plant fibre reinforced composites can replace synthetic-based plastic materials, aligning with the interdisciplinary research at the University’s Revolution Plastics Institute, which seeks solutions to the global plastics crisis.
The project demonstrated that industrial plastics can be effectively substituted with bio-based polymers such as polylactic acid (PLA) and renewable plant fibre reinforcements — including flax, hemp, jute, and date palm fibres. These plant fibres have shown excellent performance, making them suitable for various applications, from tennis rackets to smart textiles, across key industry sectors including automotive, marine, packaging and construction.
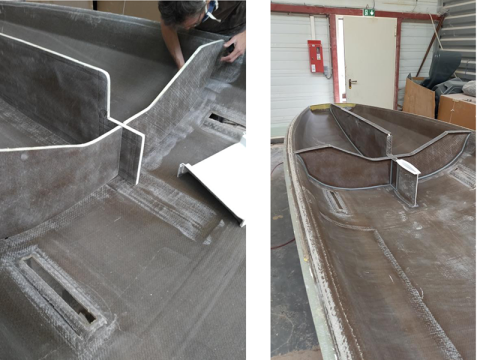
Flax foiler boat during manufacture

Completed boat made with flax fibres
Overcoming barriers and seizing opportunities
The FLOWER project navigated numerous challenges to unlock the potential of natural-fibre composites. Materials like flax offer significant opportunities to replace traditional reinforcements such as carbon and glass reinforced composites across various industries. The benefits are clear: bio-composites are recyclable, lighter than glass fibre, and contribute to reduced CO2 emissions due to their lightweight nature.
However, natural fibres come with their own set of limitations and challenges. Their properties can vary depending on their source, making them less consistent than synthetic fibres. Additionally, natural fibres tend to absorb moisture, which can affect performance. The FLOWER project has made strides in understanding and mitigating these issues, developing advanced manufacturing processes to enhance the reliability and performance of these materials.
Benefits of natural fibres:
- Renewable: Natural fibres are sourced from renewable resources.
- Less hazardous: Machining natural fibres involves fewer hazardous materials.
- Mechanical strength and high performance: Natural fibres, such as flax, are mechanically strong and demonstrate excellent performance, making them suitable substitutes for key industrial applications.
- Lightweight: Natural plant fibres such as flax, hemp and jute are much lighter than the synthetic glass fibre, contributing to the advancement of composite materials and the development of lightweight products.
- Environmental benefits: Lightweight materials require less fuel, leading to lower CO2 emissions and a reduced impact on climate change. Additionally, flax has almost four times less environmental impact compared to conventional reinforcements in composites and requires lower processing temperatures, making it less energy-intensive.
- Recyclable and biodegradable: Natural plant fibres offer greater potential for recycling and biodegradation.
Some challenges of natural fibres:
- Variability in properties: Natural materials exhibit variability in their properties depending on their source, making them less reliable and consistent compared to synthetic fibres and polymer-based materials, which are uniform and consistent worldwide.
- Moisture absorption: Natural fibres absorb moisture especially under humid conditions, leading to swelling and potential distortion in performance. Research is ongoing to understand and mitigate these issues.
- Manufacturing challenges: Developing a consistent and efficient manufacturing process for natural fibres is complex and challenging.
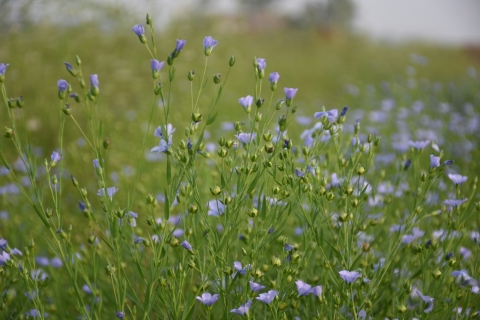
Fibres from plants, such as flax shown here, have shown excellent performance, making them suitable for various applications across key industry sectors including automotive, marine and packaging applications. Photo by Updesh Raj / Unsplash.
Measuring environmental performance
The FLOWER project emphasises the importance of a full life cycle assessment approach to measure the environmental performance of new bio-based composite materials. This is imperative for transitioning from a linear to a circular model in the composites industry, reducing waste and promoting recycling.
Recycling composite materials is very difficult. There are no clear recycling routes or waste streams for such materials. Biodegradable natural fibre materials present an opportunity to reduce waste. We’re working with the University’s Centre for Enzyme Innovation to explore different recycling options, such as chemical and enzyme recycling, and sharing our knowledge to inform future projects.
Collaboration and research-informed teaching
The project's achievements include the completion of four PhDs, the publication of over 30 high-impact journal papers, and numerous international seminars and workshops. These efforts have fostered a dynamic and collaborative research environment, with ongoing partnerships extending beyond the project's duration.
Within this project, research-informed teaching (RIT) and problem-based learning (PBL) were practiced. This inspires and encourages students to engage and solve real-world engineering problems.
Portsmouth researchers played a vital role in the project, gaining hands-on experience in sustainable materials development and innovation. We continue to work with some of the project partners, and any new materials developed are shared with students at Portsmouth.

We are expanding our research into the renewable energy sector by developing wind turbine blades using flax fibres as reinforcement
Future directions and continued innovation in sustainable materials
As a consortium, FLOWER members share and apply knowledge to different contexts. Looking ahead, we are expanding our research into the renewable energy sector by developing wind turbine blades using flax fibres as reinforcement and green epoxy as a matrix material. A partner of the FLOWER project has pledged funding to this new initiative, highlighting the success of our work and the desire to do more.
Together, we have created a demonstrator to showcase the potential of natural fibres. Typically, wind turbine blades are made from carbon and glass fibres, which require high energy for both manufacture and end-of-life disposal, with limited scope for recycling. When considering the circularity of new materials, it is crucial to balance environmental benefits against performance and end-of-life considerations.
We are also exploring the potential of another material — bark cloth. We are working with colleagues from different schools and faculties within the University of Portsmouth, and industrial partners, to consider the potential for this natural fibre to be used in packaging applications. Our research is in the business of making products, and developing solutions to tackle pollution and a wasteful, throwaway society. Portsmouth’s School of Electrical and Mechanical Engineering, Faculty of Technology is collaborating with researchers at the University of Cambridge to test these new materials at present and we will share our findings in due course.
Two of our PhD students are working on related projects. Md. Ikramul Islam is researching how textile waste can be reused in hybridized composites for advanced engineering applications, such as in the automotive industry. While Sakib Khan, a PhD student funded by Aquapak, is studying the development of sustainable, biodegradable food packaging.
Innovation in engineering is crucial for transitioning to more sustainable resource use and reducing carbon emissions. The University of Portsmouth is proud to play a key role in developing sustainable, innovative materials and minimising our impact on the planet.
You might also be interested in...
Portsmouth Centre for Advanced Materials and Manufacturing
We're undertaking fundamental and applied research in Materials Science and Engineering Technology with the focus of contributing UN’s Sustainable Development Goals.
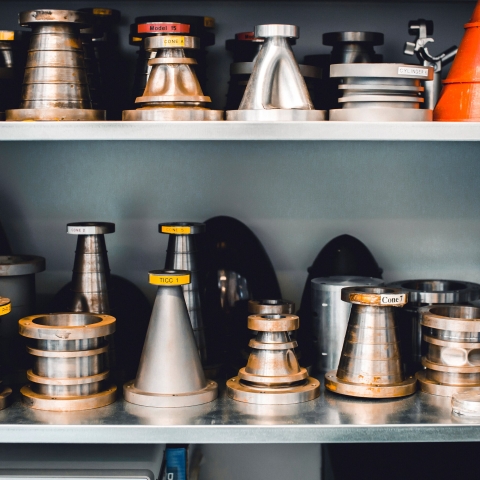
Mechanical Engineering BEng (Hons) / MEng
Influence the future of global industries through engineered products and systems. Accredited by the Institution of Engineering and Technology.
Start date: September 2025 September 2026

Centre for Enzyme Innovation
At the Centre for Enzyme Innovation, we are working to solve one of the most pressing environmental issues facing our planet.
